Glass Lamination Production Lines
Casso-Solar Technologies’ Laminated Glass Lines integrate adjustable infrared and convection heating for rapid, uniform bonding across glass types, including Low-E and coated glass. Designed with automated press roller gap settings and quick recipe changeovers, our systems support both autoclave and non-autoclave processing and accommodate interlayers like PVB and SentryGlas for consistent, high-quality output.
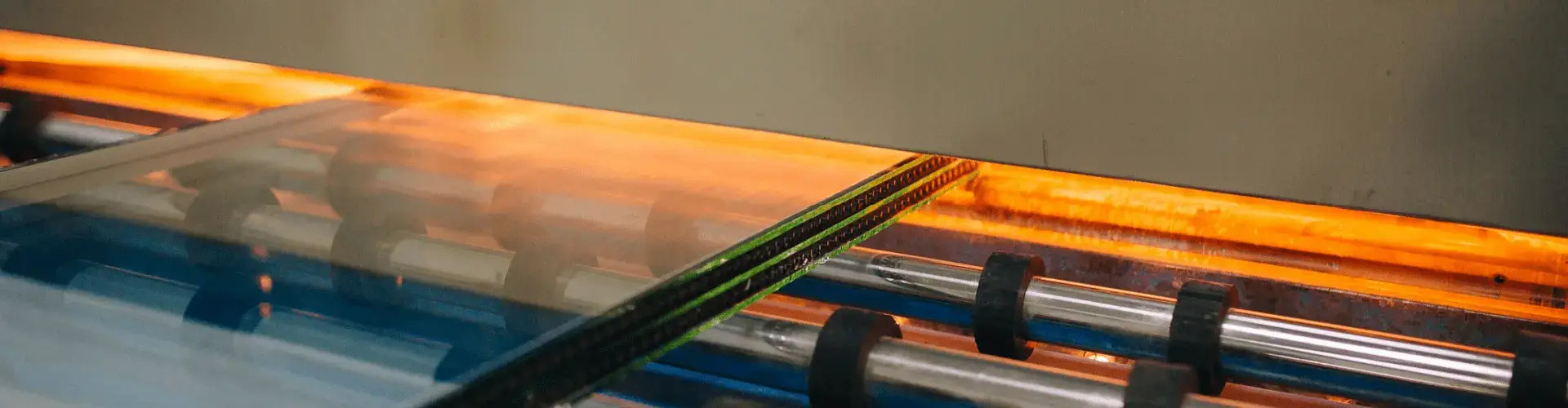
Customizable Laminated Glass Production Lines Combining Infrared and Convection for Diverse Glass Types
At Casso-Solar Technologies, our mission is to pair each customer with the piece of machinery that is best suited to their business needs. To this end, we have developed three different configurations for our Nip Roller Lamination Line, each of which is suited to a particular type of customer and product mix. As experts in both infrared and convection heating, we bring our full wealth of knowledge to the design of our lamination equipment to take advantage of the benefits of each type of heating technology. Infrared energy is able to partially pass through the glass and heat the interlayer directly, allowing for faster processing speeds, while convection heating allows for the processing of coated glass products (such as Low-E) which are IR-reflective. By utilizing both technologies in the proper combination, we are able to offer higher processing speeds while still allowing for maximum flexibility in the glass products that can be produced.
Features Common to All 3 Configurations
All of the configurations that we offer have the same basic layout for the first portion of the equipment.
Products first enter a short Preheat Oven which works to initially warm up the interlayer material and causes it to soften. Then, the products go through a first Nip Roller Press, which serves to remove any trapped air in the product.
The parts then proceed through a longer Tacking Oven which continues to heat the interlayer and causes it to begin to melt. And at the end of this common section, the parts are processed through a second Nip Roller Press, which provides the necessary pressure to seal the edges of the parts and create an initial bond between the glass and interlayer.
Additional common features include:
- Automatic press roller gap setting
- Rapid recipe changeover
- Roller conveyor with stainless steel rope-wrapped rollers
- Separate top and bottom heat control
- Minimal maintenance requirements
- High rates of energy efficiency
- Unparalleled product support from our experts
Standard Line Configuration
Our “standard” configuration is best suited for customers processing high volumes of uncoated glass. It contains only infrared heating and requires the lowest level of initial investment. While it is more limited in the range of products that it can produce than other configurations, it boasts an extremely high production rate and is capable of producing over 30,000 square feet of product per day. Products that pass through this system require processing in an autoclave afterwards before they are complete.
Low-E & Coated Glass Line
This configuration is similar in size and production rate capabilities to the standard line but includes the addition of convection heating. This allows for customers to produce coated products as well as uncoated products as the convection heat serves to compensate for infrared heat that is reflected by coated glass. Additionally, when customers wish to produce uncoated glass they are able to save energy by simply shutting off the convection heating system and using the line in the same manner as a standard line. The system adds flexibility in the types of products that a customer is able to produce, while not sacrificing the high rates of production that infrared heating is able to achieve.
Non-Autoclave Lamination Line
Casso-Solar’s proprietary autoclave-free glass lamination line is our most unique type of lamination equipment. Unlike most nip roller lamination lines that are available, this line is capable of fully laminating a part without the use of an autoclave. This means that the customer is able to avoid the high investment cost of purchasing and installing an autoclave, which can be the difference in making high-volume lamination capability affordable.
This line accomplishes the lamination of parts without an autoclave through the addition of a long Curing Oven after the second Nip Roller Press. This Curing Oven replaces the autoclave in a traditional system, saving both time and money when it comes to operating a lamination line. The Curing Oven further raises the temperature of the interlayer to a point that allows the cross-linking process to occur, fully bonding the interlayer to the glass in the same way as an autoclave.
The caveat to this process is that it only works on low-moisture interlayer products. Traditional PVB has a relatively high moisture content and cannot be processed on this type of line without first being pre-dried in a climate-controlled low-humidity environment. In addition to pre-dried PVB, this line can also laminate Kuraray SentryGlas® interlayers.
Get a Custom Infrared Solution for Your Application
With six decades of infrared technology expertise, Casso-Solar is ready to address your project needs. Reach out to our specialists today.