Polypropylene Web Heating with Various Required Heat Profiles
This case study explores how Casso-Solar's custom infrared heating system resolved temperature uniformity issues and production bottlenecks in polypropylene web processing, enabling precise heating profiles for various product widths.
The Challenge
The customer has two pieces of web processing equipment, which we will refer to as upstream and downstream, which have a 10 ft. gap between them. While the web crosses this gap it cools by approximately 10 degrees Celsus. The downstream equipment has a preheat section at the entrance to attempt to counteract this heat loss, but it is only capable of reheating by approximately 5 degrees Celsius at the desired production rate. As a result, the customer has to run the equipment slower than optimal leading to this area being a bottleneck for the entire process.
In addition, the customer has received some complaints from end users that are the result of non-uniformity in the temperature gradient across the width of the product. The existing preheat section in the downstream equipment has no ability to correct the temperature gradient.
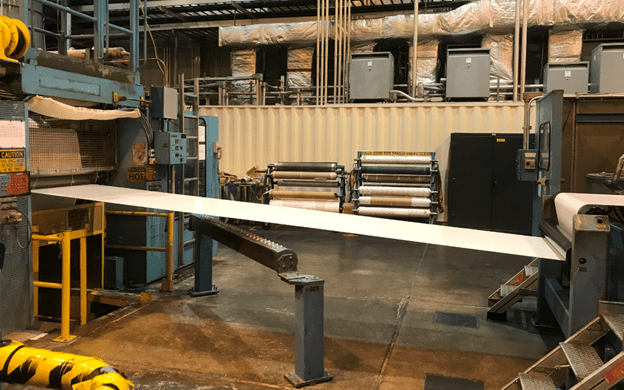
The anticipated heat profile requirements to achieve the desired temperature uniformity is further complicated by the fact that the customer runs a variety of different width products and the area of the web requiring additional heating is very narrow (2-3” wide).
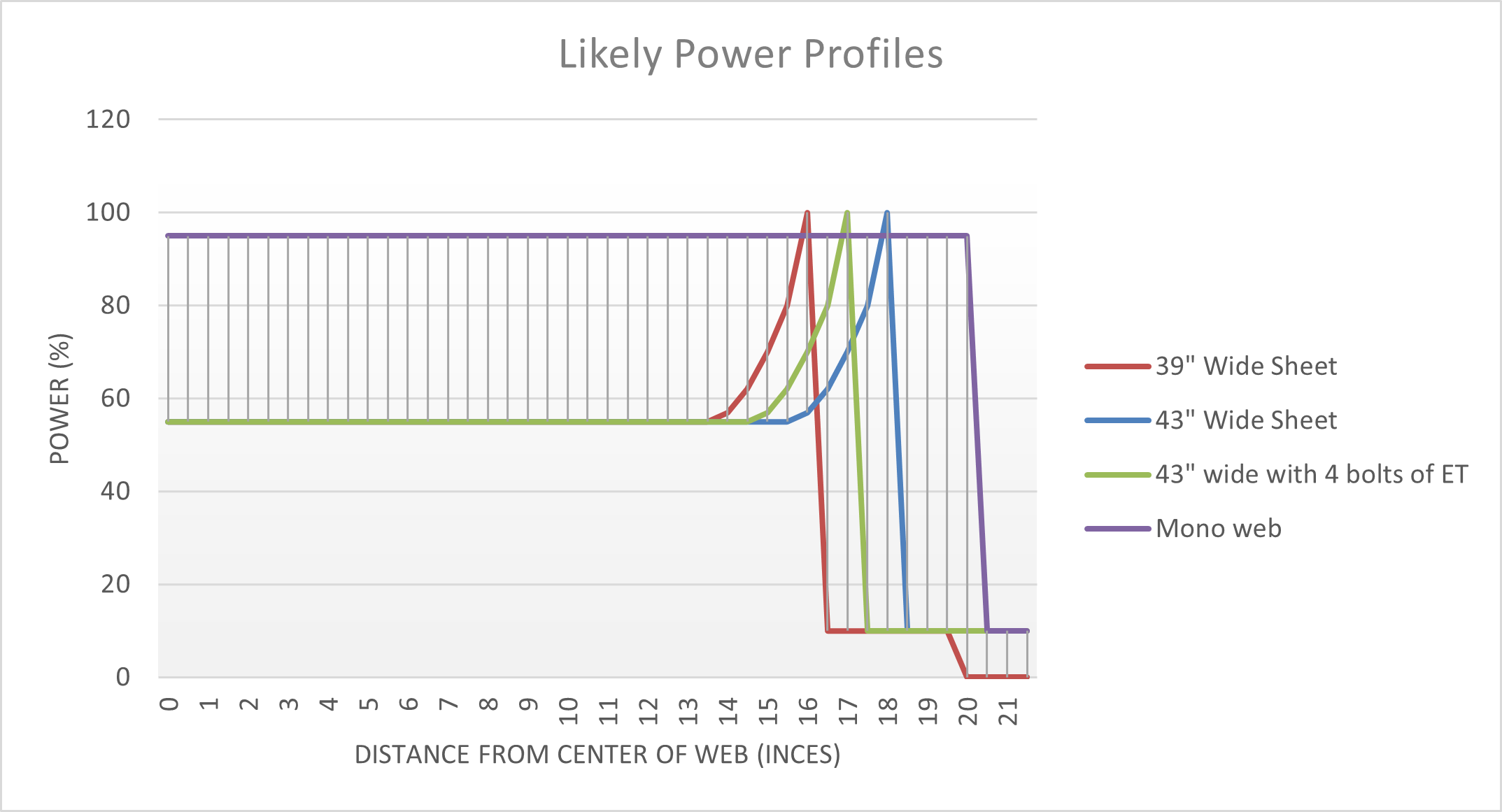
The Solution
Casso-Solar proposed, designed and built an infrared heating system equipped with our V-series infrared heaters with each heater having a total of (29) zones: (1) large center zone and (14) 1” wide edge zones on either side of the center zone. This gave the customer the ability to create precision heating profiles specifically suited to fit each of their various product widths.
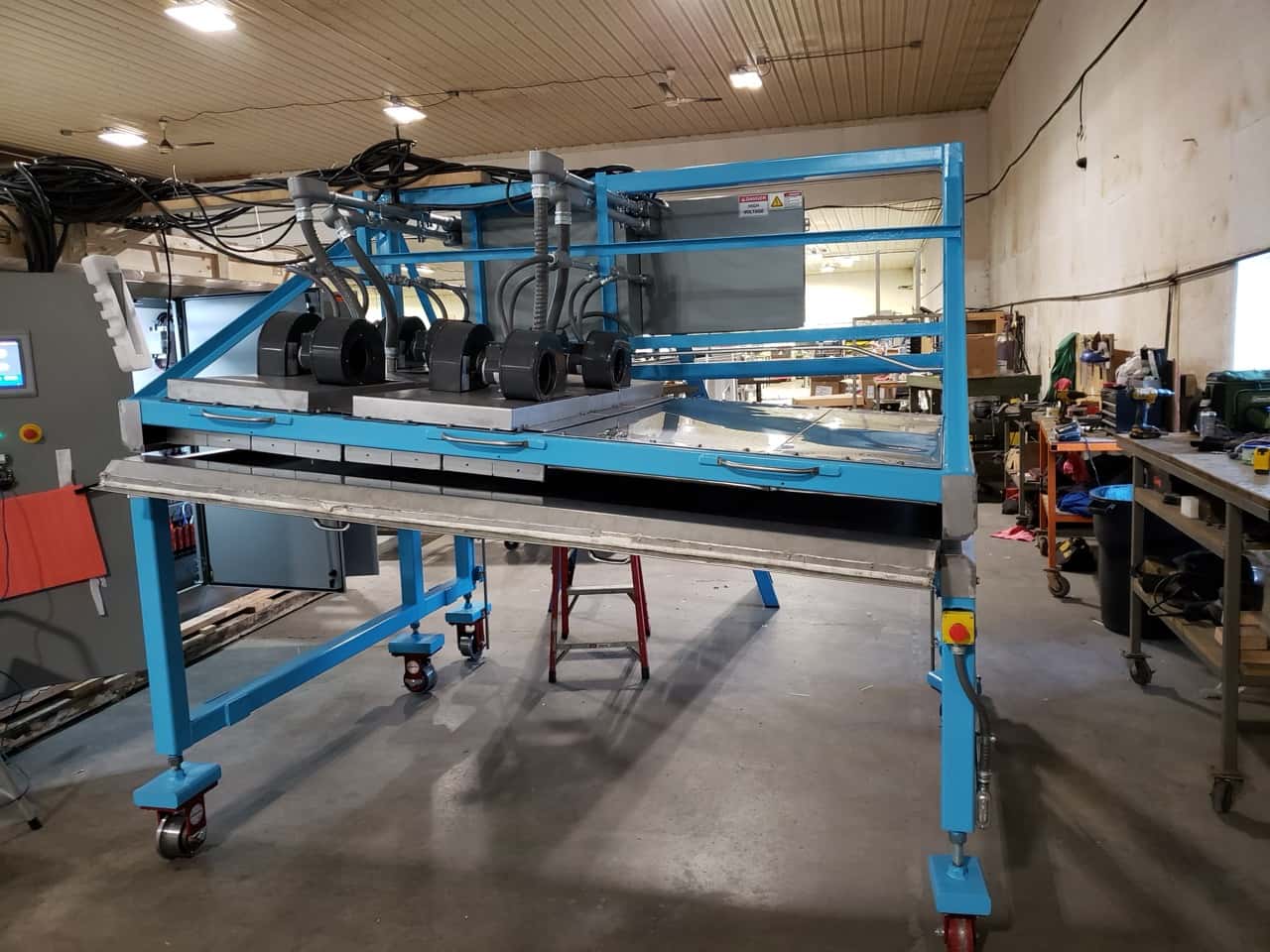
The new system only needed 4’ of heating in the direction of travel to accomplish the required reheating at the desired line speed, so the customer opted to have Casso-Solar design and build the equipment and control system at a total of 8’ in length but only install 4’ of heating. This provided them with the flexibility to easily add additional heaters in the future if they are able to increase their production rates, meaning that this area is no longer a bottleneck and won’t be one in the future either.
Some noteworthy features that were included:
- PLC (Programmable Logic Controllers) control with recipe storage to allow for one-button setup of heat profiles when changing product width and/or composition
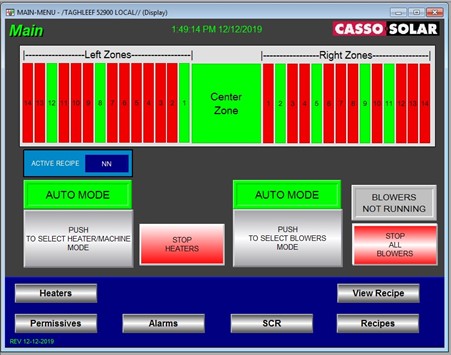
- V-series heaters were equipped with cooling blowers that activate during a line stoppage to prevent the web from overheating
- Hinged side insulation panels to allow for easy access for rethreading operations
- Entire system is installed on linear rails to allow it to be moved offline for maintenance
Contact our Sales Team to discuss our extensive offerings and find out how we can deliver equipment custom-designed for your needs.