Nip Roller Lamination Systems
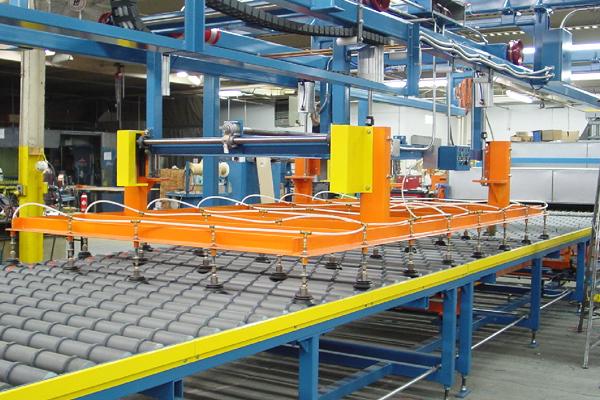
Introduction
Laminated glass serves an important role in our society and has numerous applications in security, architecture, construction, and more. In addition, the profit per square foot is far higher than monolithic glass allowing manufacturers to increase their margins. Using high-quality glass lamination equipment is of paramount importance to produce laminated glass at a high rate while also meeting industry quality standards. Nip roller lamination systems are the answer to how to accomplish this. Casso-Solar nip rollers lines work by alternating infrared heat to soften the interlayer with large diameter nip rollers to press and tack the assembly together. This post discusses the factors to consider for nip roller lamination and the benefits of using this method.
Factors to Consider When Using Nip Rollers for Lamination
When laminating sheets of glass into a single assembly, there is a possibility of air remaining trapped inside when not done properly which leads to bubble formation. Nip rollers help remove the trapped air, but some nip designs are better and more consistent than others. Some crucial things to consider when looking at lamination equipment are:
- The nip roller system design should be such that absolutely no air can be trapped inside after the lamination process.
- It should work for all types of products and there should be no rejects due to breakage from excessive pressure.
- Lamination pressure when the glass passes through the nips rollers must be consistent and even across the entire surface of the glass.
To achieve this, Casso-Solar designs our nip roller systems with the following features:
- 17” diameter EPDM rubber-covered nip rollers, which are larger than most competitors in the industry. This allows for a longer period of contact with the assembly when it passes through the nips, ensuring the maximum amount of air is removed.
- Rollers are driven together off of the same drive chain to ensure no slippage between the top and bottom roll.
- Rolls are covered with ½” thick EPDM rubber and grooved. These factors ensure the best combination of grip, pressure and ability for trapped air to escape.
- The gap between the top and bottom roller is automatically controlled by PLC driven recipes to ensure consistent settings for the entire run.
- The alignment of the rolls is guaranteed by large linear guides that ensure the parallelism of the rolls to one another.
- Easily adjustable pressure from an operator interface on the HMI screen allows for quick changes for different products.

Benefits of Nip Roller Lamination Systems
Although there are other methods of lamination such as vacuum bags, nip roller lamination systems offer a few advantages:
- Significantly less labor is required per part produced; simply place a piece of interlayer between two equal size pieces of glass and send it through the nip system. Place the part in an autoclave to finish the process
- Far higher production rates are possible. The biggest and fastest vacuum bag systems can produce around 2000 sq. ft. of glass a day. A standard nip roller system can produce ten times that amount in a single shift.
- Lower reject rates. Because vacuum bag systems are labor intensive they lend themselves to more human error and thus higher rates of scrap.
Are you looking for a nip roller lamination system for your glass manufacturing unit? If so, contact Casso-Solar Technologies and with our extensive experience designing and building nip roller systems we will provide you with everything that you need.