Glass Lamination Systems
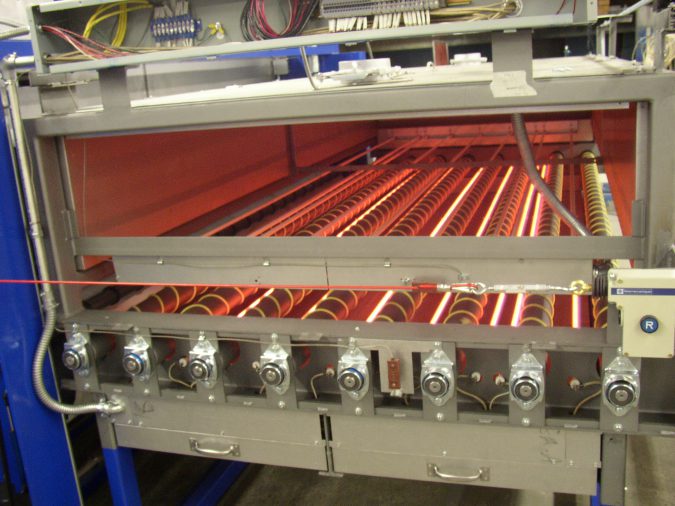
What to know before you buy
By: Derek Burkholder
Laminated glass is a high value-added product that more and more companies are moving to producing in-house rather than relying on out-sourcing.
The addition of laminated glass production for any company is a major investment, so it is critical to ensure when purchasing equipment that it is designed to produce the products a company wishes to sell, while also being cost-effective to operate.
There are many components to a laminated glass production line, such as the washer, cleanroom and autoclave. Where there is the most variety in equipment are the oven and press designs.
Every equipment manufacturer has a different approach to the design of their ovens, but all tend to use one of three methods of heating: convection, infrared (radiant), or a combination of the two.
This article seeks to explain the differences between the three oven designs and examine the benefits of each.
CONVECTION
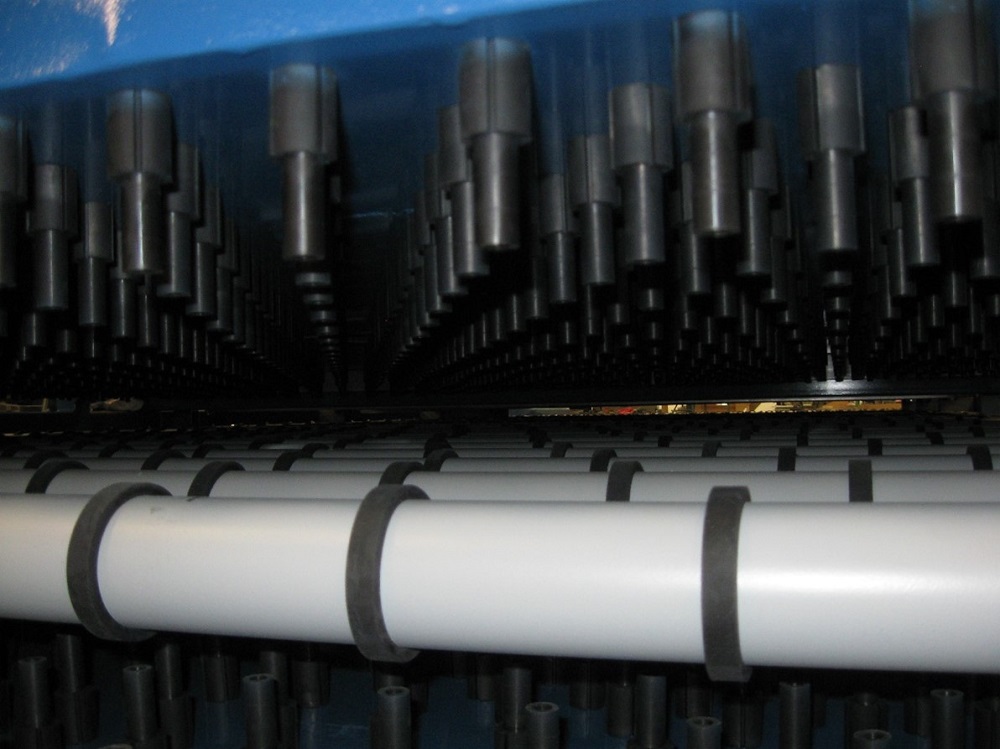
Convection heating is the most familiar method, as it is the way that most home ovens operate. Sometimes called “hot air heating,” in this type of oven air is heated up to the desired temperature and then distributed throughout an insulated chamber. To maximize efficiency the air is typically recirculated through the system to minimize losses and operating costs. Once the oven reaches the desired operating temperature and power level to raise the temperature of the laminate, it requires a reasonably low amount of energy to remain at the desired temperature.
As parts pass through the insulated chamber, a heater (either gas or electric) will heat the air. The hot air heats the surface of the glass, and the heat then conducts through to the center of the laminated assembly to the interlayer. Thus, the primary factor affecting production rate is the thickness of the assembly. The thicker the assembly, the longer the heat will take to reach the interlayer at the center.
Heating efficiency is also impacted by the design of the air delivery system (nozzles, air knives, slots, etc.), as faster delivery of larger volumes of air leads to more efficient heat transfer.
INFRARED
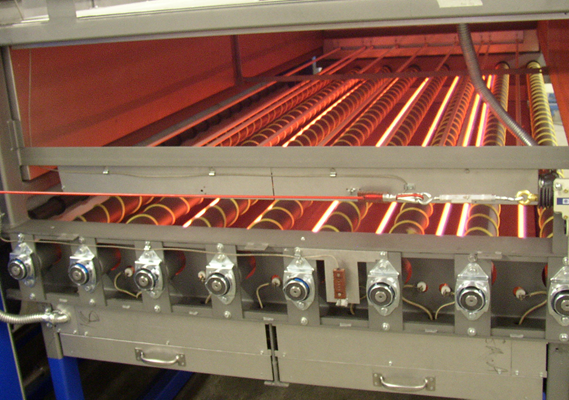
Infrared heating utilizes radiant energy to transfer heat to the product. Radiant heat transfer relies on the principle that all hot objects radiate heat to their surroundings in the form of electromagnetic waves.
Colder objects then absorb this infrared energy to varying degrees based on their particular absorption spectrum curve. Air, for example, does not absorb most wavelengths of infrared energy and instead allows the energy to pass through it, while glass and interlayer materials such as PVB absorb the majority of infrared energy.
This means that energy produced in an infrared lamination oven is primarily absorbed by the laminated assemblies and is not lost to the air, allowing the product to be targeted efficiently.
Another benefit of infrared energy is that unlike convection heat it is capable of penetrating into objects to heat them from within, rather than just from the surface.
For glass, infrared energy penetrates approximately ¼ inch into the material before being fully absorbed. This allows for thicker parts to be heated more quickly as the energy does not have to conduct as far to reach the center of the assembly.
The increasing prevalence of low-e and infrared reflective coatings has had an impact on the use of infrared heating in glass lamination. Because these coatings are designed to reflect infrared energy, it necessitates the use of a different heating technology to compensate.
This leads us to hybrid convection/infrared ovens. Convection or convection/infrared is a must for the coated or top side of the product. Infrared only is most efficient on the bottom or uncoated side.
HYBRID CONVECTION/INFRARED
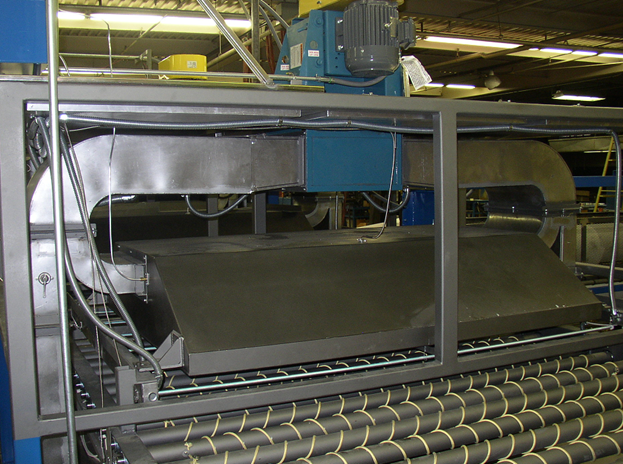
As the name implies, hybrid convection/infrared ovens utilize both convection and infrared technology to provide the benefits of both heating methods. These ovens can often be run using infrared only when producing uncoated glass and then can have the convection heating technology activated when infrared-reflective coated glass is being produced.
This allows a manufacturer to maximize production efficiency by using the heating technology that is best suited to the type of product being manufactured at a given time. Systems can be programmed through the PLC, programmable logic control, system to provide the correct setup for each product run.
COMPARISON
Each type of equipment comes with benefits which are outlined in the table.
A convection system is well-suited for companies that are constantly producing a variety of coated and uncoated products simultaneously or for companies that wish to keep operating costs down.
The trade-off is the production rate. For the same size equipment, a convection system will run slower than a system equipped with infrared heating as it will require the laminates to stay in the oven for a longer period of time to reach the required temperature due to the slower rate of heat transfer.
In order for a convection-only system to achieve a similar production rate, floor space would need to be sacrificed to allow the line to be longer.
Infrared-only systems are best used when 80 to 100 percent of a company’s planned production is uncoated glass in large quantities. This type of system offers the fastest production rates while being relatively easy to operate. It also is the fastest at warming up and changing settings.
For a company that wishes to produce all types of products while also maintaining the highest level of production possible and minimizing floor space, a hybrid convection/infrared system is the ideal solution.
A hybrid system offers the best of both technologies since it combines high rates of production with the flexibility to produce both coated and uncoated products.
FUTURE REQUIREMENTS
When making any significant equipment investment, it is of course important to consider both a company’s current and future needs.
An infrared-only system might be the perfect fit for current production requirements of strictly uncoated glass, but it will need to be modified if future plans call for significant coated glass production.
Similarly, a convection-only system might accommodate current sales volume, but if sales increase, a longer oven will be needed to allow the line speed to increase accordingly.
A hybrid system provides both high production rates and flexibility in the types of products that can be produced, which could protect from the need to upgrade the equipment as time passes.
Article Originally Published in Glass Magazine May/June 2022 Issue. Original Article Link: https://www.glassmagazine.com/article/glass-lamination-systems