Catalytic Infrared Paint Curing System Discussed
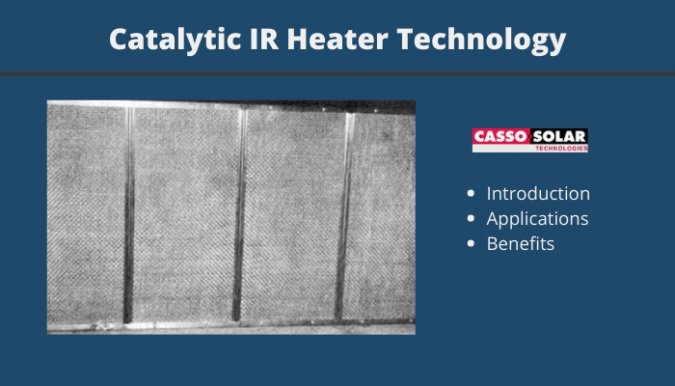
Introduction
Catalytic infrared (IR) paint drying/curing systems are used in several industries for drying coatings that have high solvent loads. The catalytic IR curing systems are different than conventional electrical IR dryers in that the main source of energy comes from natural gas or propane rather than electricity. This post gives insights about what catalytic IR drying technology is and in what applications it is most useful.
Quick Introduction to Catalytic IR Heater Technology
Catalytic IR heater technology is used to provide flameless drying or curing while using a fuel as the source of heating. The fuel supply is passed over an electrically pre-heated catalyst (such as a platinum coated pad) which causes a heat-producing chemical reaction. This heat is given off from the catalyst in the form of medium-to-long wavelength energy that can be direct absorbed by the target object. This reaction is completely flameless and primarily gives off only water vapor and carbon dioxide as byproducts.
Catalytic IR Paint Curing System Applications
Many companies have limited electrical supplies in their facilities leading them to mainly use gas-fired systems for their heating needs. Lack of a significant electrical supply traditionally led a company to forego switching from a gas-fired convection system to a more efficient electric IR curing system. A gas catalytic IR curing system can bridge this divide and allow a company to continue to utilize their existing fuel supply for heating while also providing the efficiency of an IR-based system.
The other main reason for switching to gas catalytic IR heating is for use in high-solvent load applications. Because catalytic IR heaters produce heat with flameless technology, the risks inherent in a gas-fired convection system (where combustion is used to achieve heating) can be avoided.
Benefits of Using Catalytic IR Paint Curing System
This method offers several benefits over conventional paint drying systems.
- Being 100% flameless technology, it can be used for high-solvent load applications.
- Catalytic heaters are largely maintenance-free, significantly reducing equipment upkeep costs.
- It can utilize an existing natural gas or propane fuel supply to provide more efficient heating.
- The byproducts from the catalytic reaction are primarily water vapor and carbon dioxide, a much more eco-friendly solution than combustion technology.
- Because the heat produced is delivered via infrared, the efficiency of heating is higher as more energy is directed into the product rather than the surrounding air.
The benefits and ease of switching from a conventional gas-fired oven to a catalytic one make this an excellent financial decision. Casso-Solar Technologies provides catalytic infrared heating systems for a variety of heating and curing applications. These systems are provided in custom configurations with accessories such as complete PLC-based PID temperature control systems, complete gas trains, face grills, LP tanks, regulators, and so on.
Related Blogs
- Why Infrared Quartz Heaters are More Efficient than Ceramic Heaters?
- Know the Industrial Applications and Benefits of Infrared Heaters
- Quartz in Infrared Heater Design: Why Is It Used and How Does It Work?
- Gas Catalytic Infrared Heaters: Why They Are Used for Solvent Curing?
- Types of Industrial Electric Infrared Heaters Offered at Casso Solar Technologies: Part 2
- Types of Industrial Electric Infrared Heaters Offered at Casso-Solar Technologies: Part 1
- Guidelines for Maintaining Industrial Drying Systems