An Overview on Applications of Infrared Heaters in the Glass Industry
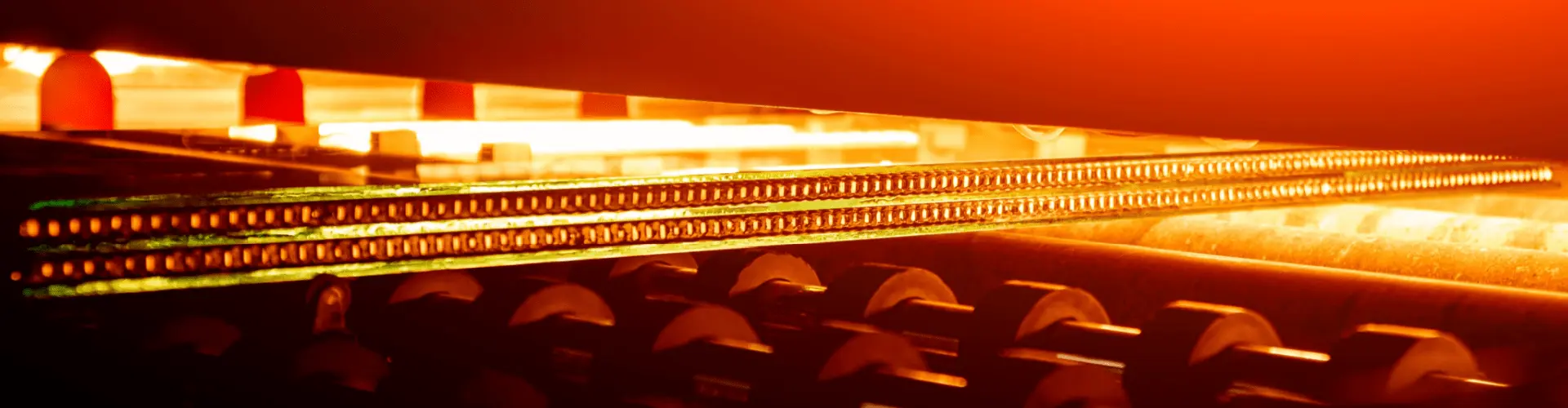
Precisely controlled heating is an important aspect of many industrial processes and is used in many glass manufacturing processes. Infrared heaters can heat surfaces directly and precisely, with high efficiency. They are easily controlled to achieve desired thermal profiles, and accurately adjusted to process and material requirements. Infrared heaters are widely used for drying paint and other coatings on glass, processing laminated glass, glass annealing, and bending, among other applications. The focus of this post is to highlight the ways that infrared heaters are utilized in glass processing.
How Are Infrared Heaters Used for Glass Processing?
Infrared heating technology provides a finer level of control and efficiency than most other heating technologies in the market. They are widely used for the following glass processing applications:
- Automotive Glass: In the automotive industry, infrared ovens are used for screen print drying, glass bending, and laminating, mainly.
- Architectural Glass: This industry utilizes infrared heaters in nearly all applications. Infrared heating is used during lamination, bending, casting, and glass decoration. Decorated glass sheets are printed with different types of inks, such as ceramic, silicone, urethane, and enamel to create impressive decorative patterns. This printing is performed using screen printers, roll coaters and digital printers and then dried and cured with infrared.
- Appliance Glass: Today, it is common to find decorated and durable glasses in a multitude of appliances. The glass sheets are cut and bent into desired shapes and heat-treated for strengthening. Infrared curing and drying systems are used for curing various types of inks and hard coatings. Many of these application glasses are fired with water-based, terpinol, water-miscible, and pine-oil based inks. Since many of these coatings have different drying and curing properties, they require a drying oven with a high degree of control flexibility, which can easily be provided with infrared zoning.
- Aircraft Glass: Windshields on commercial aircraft are highly engineered parts that must meet strict standards for safety. These glass windshields are created by bending multiple layers of glass at the same time to the same profile. This bending is achieved using precisely controlled and zoned infrared heaters which are placed above and below the part.
- Ballistic Glass: Bullet resistant glass is typically made from laminated polycarbonate and glass. Infrared heaters can be used in several steps of this process. The polycarbonate material is sandwiched between the two sheets of clear glass and laminated using infrared heaters. If being used in an automotive application, the glass is usually bent on ring molds or a full surface molds using infrared heat. The precise heat control ensured by the infrared heaters helps minimize the gaps between the layers of glass during the bending process.
- Fragrance Bottle Glass: Perfumes and other fragrances are usually sold in glass bottles with brilliant coatings and decorations. Infrared ovens are used to dry paints on these glass bottles.
- Photovoltaic Glass: Photovoltaic glass is used in an increasing number of applications as the technology becomes more mainstream. Special types of coatings are applied to the glass to improve their beneficial properties. The coatings can be dried using infrared drying or curing oven systems. This glass is often laminated as well, which as noted previously is an application where infrared can be very beneficial.
It is important to use the right type of infrared heater or oven for glass processing as each application is unique. When you source your infrared heat processing equipment from trusted manufacturers such as Casso-Solar Technologies, you can be assured that you are getting the proper equipment to do the task at hand. We have the expertise and experience to produce customized infrared systems to meet your application requirements.