All Important Question Answered About Infrared Ovens
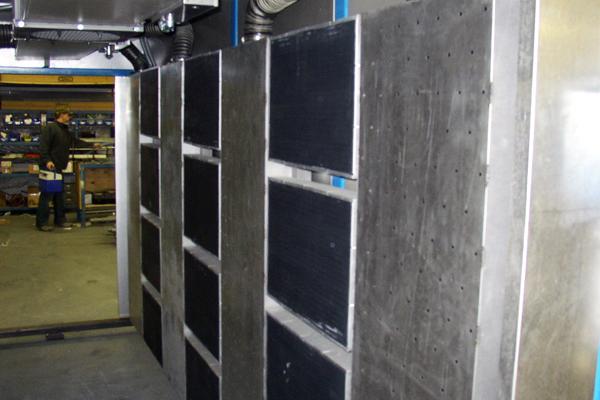
Introduction
Infrared ovens are widely used in a variety of industries as a more efficient alternative to convection ovens. They are used for various heating processes in the manufacturing sector such as baking, bonding, pre-heating, thermal-forming, laminating, and many others. Infrared is a form of electromagnetic energy which can be used to efficiently heat objects because air does not absorb much energy in the infrared spectrum. Thus, IR ovens perform tasks faster than traditional ones since the energy produced heats the object directly and is not wasted heating the air. Would you like to know more about infrared ovens or how infrared heat processing works? This post discusses some of the most common questions asked about infrared heating.
How Does Infrared Process Heating Work?
Infrared heating works by transferring energy via electromagnetic waves directly from the heating elements to the target. Infrared energy waves mostly fall within the 1-8 micron range. This range also happens to be the set of wavelengths at which most materials readily absorb energy. Additionally, air does not absorb much energy in this range of wavelengths, thus drastically reducing the amount of energy lost to the oven environment. The combination of these two factors results in a very high efficiency as the vast majority of the energy used is directly transferred to the product with minimal losses. This provides a major advantage over traditional convection ovens as infrared systems take up less valuable floor space due to lower insulation requirements.
Which Wavelength/Temperature is Required for an Infrared System?
The wavelength of infrared energy is longer at a lower temperature and shorter at higher temperatures. The temperature/wavelength that is required to process a product entirely depends on two factors: the material being processed and its thickness. Every material has its own spectral absorption curve that dictates how much energy is absorbed at varying wavelengths and thicknesses. By designing an infrared heating system that is specifically tuned to operate at the optimal wavelength for a material, heating time and energy use can both be minimized. Infrared heating elements can be much more finely controlled than convection heaters, allowing the system to operate at a specific wavelength with little to no fluctuation. Casso-Solar Technologies maintains a lab facility specifically for determining the ideal wavelength and heater design for a given product.
Why Choose Infrared Systems?
There are many reasons to choose an infrared heating system over a convection-based system, including but not limited to:
- Higher degree of adjustability on heat output to allow for use with multiple products
- Improved quality control resulting in reduced reject rates
- Less heat lost to the environment
- Increased throughput
- Faster warm-up and response times
- Low maintenance
- Minimal floor space requirements
- Lower carbon emissions
What Are the Common Application Areas of Infrared Ovens?
Some of the more common applications for infrared ovens are found in the following industries:
- Glass Processing
- Paint and Powder Finishing
- Textiles Manufacturing Processes
- Plastics and Films Manufacturing
- Metal Manufacturing Processes
Are you considering a switch to an infrared heating system? Casso-Solar Technologies is a leading equipment manufacturer that can help. Our highly trained sales staff will listen to your application needs and determine the appropriate solution. In operation since 1960, Casso-Solar Technologies has the experience required to supply high-quality infrared equipment according to your specifications.